Npi Costing Lead Job in Caterpillar
Job Description
Description
Job Title: NPI Costing Lead
Role:
The NPI Costing Lead is aleadership cum individual contribution role, bringing technical expertise andguidance on supporting/improving cost effectiveness of new products deliveredby the NPI process working closely with a cross-functional team comprising engineering,purchasing & costing.
Leadership:
Projectleadership is the prime focus. Will have to execute projects through extensivecollaboration, technical guidance to team for scope clarity & clearingroadblocks.
Job Duties/Responsibilities mayinclude, but are not limited to:
Plan andmanage the job/project; -Manage the business/financial aspects of the job orproject; Be a spokesperson of the team.
Provide asupportive work environment for the team;
Mentor,coach, and develop others; and manage ones own development.
Keycustomer focussed & must understand critical customer requirements.
Usetechnical expertise and product knowledge to play the leadership role in theOptimization projects with innovative solutions.
Supportand advise other engineers of Cost Analysis team, other Product Developmentteams and suppliers.
Provideexpert opinion on the Cost modelling and Optimization effort.
Own the productcost delivery along with the cross functional NPI teams, drive functional costreviews.
Devisethe strategy for cost reduction though data analysis, should costing, designchanges & negotiation.
Work withthe product/NPI managers & BR teams to set the right cost targets for NPI.
Work withthe cross-functional teams to ensure correctness of the cost roll up.
Provideleadership in the implementation of cost reduction actions throughout the NPIcycle.
Generatecost reduction actions & ideas and work with Purchasing & Design teamsfor implementation.
Audit andestablish standards, policies and practices relating to quality, costreduction, in performing cost modelling and optimization.
Stayabreast with variable & material cost movement to provide value inmanufacturing strategy for a cost standpoint.
Providelevers to Purchasing for negotiation & participate in critical negotiationswith suppliers.
Providecost analysis, cost walk, trade-off analysis of cost vs features in NPI reviews.
Researchand develop new technology in the area of manufacturing.
Play therole of a SME in team meetings / discussions.
Decision making:
Has farreaching impact on project team/immediate workgroup/division/BU/suppliers/customers/CATmarket.
Managefinancial/business aspects of deliverables.
Coach& mentor team members to get better performance.
Learning & Development:
Incumbentmust manage their own development, continuously learning through experience newbusiness knowledge and skill, interpersonal and leadership skills, andunderstanding the customers needs and application of the product or process,as well as keeping up with technology.
Technical Competencies:
ProcessPlanning - Devises process plans to include work standards, standard work,planned method cycle time and quality control plans.
TechnicalProject Management - Manages project work and project teams to solve technicalissues and meet commitments. Includes the ability to use project managementtools to control time, cost and quality objectives and to clearly communicatethese objectives to all team members.
ManufacturingProcess Comprehension - Comprehensive knowledge and experience of manufacturingprocesses for construction equipment Heavy & light fabrications,hydraulics, electrical & electronics, cabins, engines & aftertreatment.
TechnicalAcumen - Print reading includes geometric dimensioning and tolerancing, SixSigma, CPS/Lean principles, data analysis, general computer and informationsystems (utilizing various MS-Office 360 tools).
NewProduct Introduction (NPI) - Understanding of 8 phases of Caterpillar's NPIProcess (Strategy, Define, Measure, Explore, Design, Verify, Pilot andProduction) to deliver quality services to customers.
ToolDesign and Selection - Effectively applies appropriate tools and methods for agiven process such as assembly, machining, welding & fabrication.
FunctionalManufacturing Expertise - Knowledge in the tenets of lean manufacturing, andEnterprise Excellence processes, best practices, and tools.
Tools& Expertise: Product Data Management (Teamcenter Engineering), Creo,Costing knowledge like material rates, work centre rates, labour and overheadsetc., Product Knowledge -Machines and Engines, Knowledge on Costing Softwareusage.
Qualifications
RequiredQualifications:
Bachelor degree (orequivalent) in an accredited Engineering (must be from Mechanical/Automotiveengineering streams) with 15 to 20 years of relevant work experience (Design &Development, Manufacturing, Product Costingetc. of Earthmoving/Construction Products like Dozers, Motor Graders,Pavers, Compactors, Road Processing machines, Excavators, Back-Hoe Loadersetc.).
Strong analyticalskills.
Proven teamleadership skills.
Global workingexposure.
Analysis,Communication, Decision Making, Initiative, Innovation, Team work, Technicalknowledge, Project Leadership.
Desired Qualifications:
Mastersdegree (or equivalent) in an accredited Engineering (Mechanical engineeringwith specialisation in Machine/Product Design, Automotive, Applied Mechanicsetc.).
Goodcommunication, interpersonal and collaboration skills.
Caterpillar is an Equal Opportunity Employer (EEO)
EEO/AA Employer. All qualified individuals - including minorities, females, veterans and individuals with disabilities - are encouraged to apply.
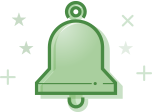
