Director Tisc Bottling Capabilities Development Lead Job in Coca Cola Careers
Director Tisc Bottling Capabilities Development Lead
- Gurgaon, Haryana
- Not Disclosed
- Full-time
SUMMARY The Bottling Manufacturing Capabilities Development Director is responsible for overseeing the planning, development, and implementation of innovative and efficient manufacturing & Governance capabilities by working with bottling partner HR leads to optimize and safeguard the bottling process, while creating an inclusive culture of continuous improvement. The Director leads the network with system stakeholders such as bottling organization, OU, corporate and external agencies to build capabilities and identify opportunities for improvement and ensure that the bottling community achieves and evolves their enterprise maturity objectives from a talent, structure, capabilities, and digitalization perspectives. This role focuses on designing and optimizing the technical organization structure along with the talent strategy for strengthening bottler capabilities. Further, the incumbent will be responsible to shape, implement/evolve the people processes to help bottling organization meet its strategic goals. Their role is to create an integrated and agile TISC bottling organizational framework that encourages efficiency, innovation, and adaptability. KEY RESPONSIBILITIES Develop and implement a strategic plan for capabilities development in the bottling manufacturing process. The role involves creating an integrated and agile organizational framework that encourages efficiency, innovation, and adaptability. Assess the existing bottling organizational structure, processes, and culture to identify areas for improvement and opportunities for greater efficiency. Design or recommend in collaboration with system network, fit for purpose organizational structures, processes, and models to optimize performance, innovation, and adaptability. Leading or overseeing change management initiatives to ensure a smooth transition and integration of new organizational designs. Develop and implement performance measurements and key performance indicators (KPIs) to track the success of organizational changes and improvements. Develop and manage talent, ensuring a continuous pipeline of skilled employees, and fostering an environment of learning and skill development. Lead the identification, evaluation, and prioritization of opportunities to improve manufacturing capabilities, including the adoption of new technologies, equipment, and processes Collaborate with cross-functional teams, including production, quality assurance, and maintenance, to design, implement, and optimize manufacturing processes that maximize efficiency while maintaining product quality and safety. Develop and enable the implementation of training programs to ensure that all personnel are equipped with the skills necessary to achieve performance goals. Staying current with external trends, innovations, and best practices in organization design, change management, and related fields to better inform decision-making. Managing resources, budgets, and timelines for organization design projects, making sure that interventions deliver maximum value and have a positive impact on the organization's overall performance. Stay informed on the latest industry trends, innovations, and best practices in bottling manufacturing to ensure continued improvement within the organization. QUALIFICATIONS Bachelor's degree in engineering, manufacturing, or a related field; advanced degree is a plus. Prior experience in HR/Talent roles in a manufacturing setup can also be considered Minimum of 8-10 years of experience in manufacturing, with a focus on bottling operations, process improvement, and capability development Strong record of leading and accomplishing complex franchise transformation and leadership initiatives Proven track record of leading successful manufacturing capability development projects. Demonstrated ability to manage cross-functional teams and collaborate with stakeholders at all levels Strong analytical, problem-solving, and decision-making skills. Excellent written and verbal communication skills. Knowledge of industry standards, regulations, and best practices in bottling manufacturing processes. Familiarity with relevant tools, technologies, and equipment used in bottling manufacturing operations Experience with budgeting, resource allocation, and project management in a manufacturing setting. Ability to adapt quickly to change and drive innovation in a fast-paced environment.
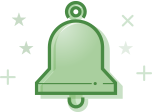
